ESG Topics A-Z
Human rights
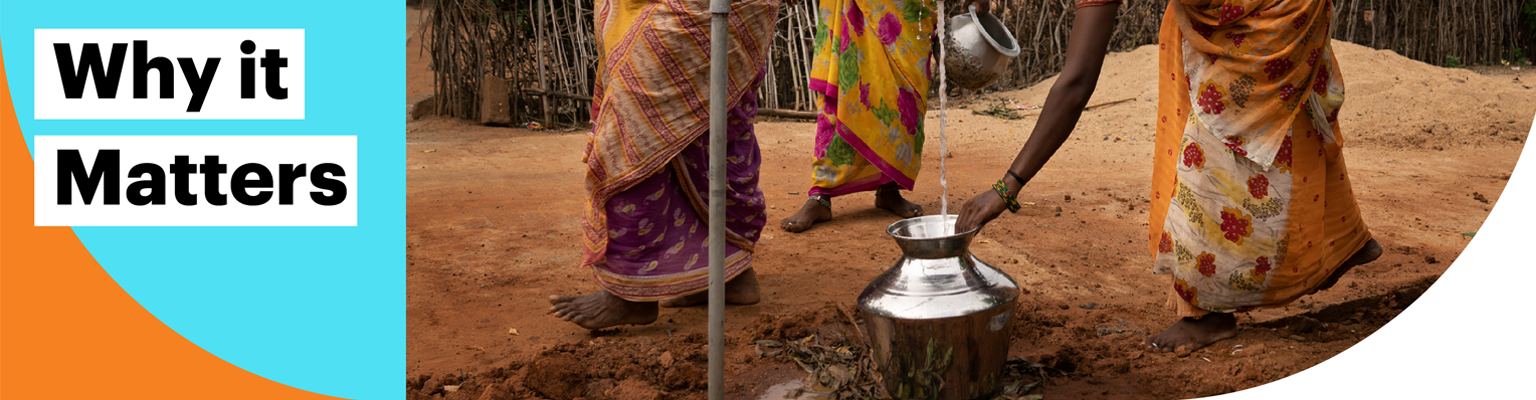
To PepsiCo:
Human rights abuses of any kind are unacceptable. PepsiCo can be a positive influence, promoting respect for human rights across our supply chain and aiming to take action to help address impacts wherever we uncover them.
To the World:
All people have the inalienable right to life, liberty, work and education, as well as the freedom to express opinions, the freedom of association and the freedom from slavery and torture. These and other fundamental human rights are enshrined in the Universal Declaration of Human Rights and the International Labor Organization (ILO) Declaration of Fundamental Principles and Rights at Work. Challenges nevertheless exist in achieving consistent respect for human rights around the world — from interference with the rights of workers to legal restrictions on the right of association.
Approach
We are a global company with a complex supply chain that spans multiple tiers, hundreds of countries and territories. A management approach is required as we work to help prevent, identify and address potential human rights impacts throughout our operations and direct supply chain. Our approach is grounded in the United Nations (UN) Guiding Principles on Business and Human Rights (UNGPs) and is based on the following pillars:
Salient issues
With this approach as our foundation, we prioritize our efforts by focusing on our salient human rights issues — the human rights at risk of the most severe negative impacts through our company activities. This process aims to develop appropriate policies and procedures to help prevent and address potential human rights risks within our business and supply chain. We closely monitor emerging issues and regularly review our salient issues in an effort to align with emerging best practices and external stakeholder feedback.
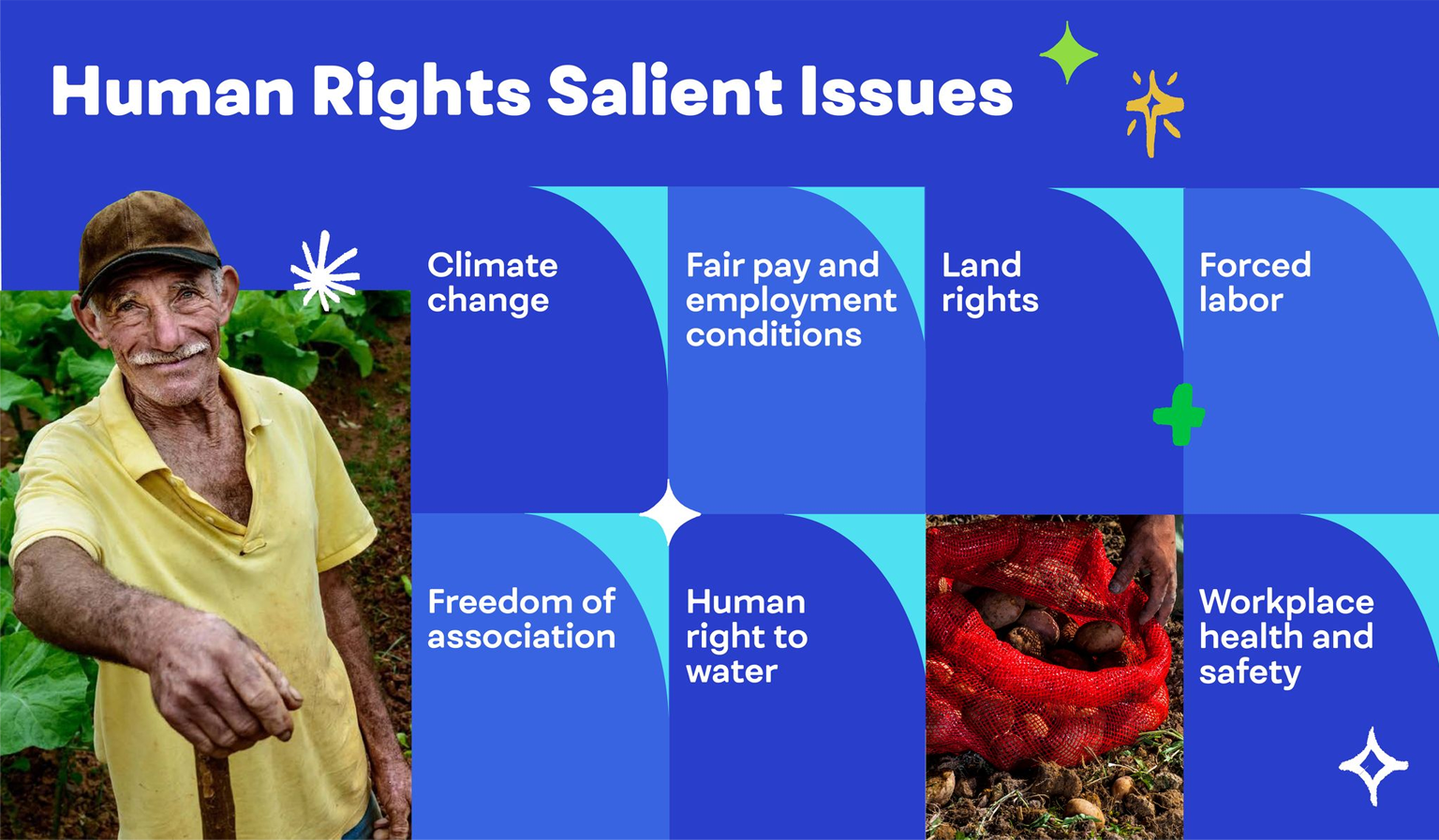
Climate change
Climate change and human rights are inextricably linked, and we recognize that the direct and indirect effects of climate change are often felt by the most vulnerable people and groups among us. We have, and plan to continue to embed a human rights lens into our climate change mitigation and resilience efforts to help respond to potential climate-related human rights impacts.
Fair pay and employment conditions
Given the complexities of the manufacturing and agriculture sectors, workers in these industries are at a higher risk of facing potential adverse human rights impacts related to working conditions and fair pay, such as excessive working hours and lack of adequate rest periods. We believe that everyone should earn a wage sufficient to afford a decent standard of living, and we have established several initiatives aiming to help advance fair pay and employment conditions throughout our direct operations and supply chain.
Land rights
Secure land rights are a vital component of economic prosperity, sustainable food production and the responsible use of natural resources. Land rights issues have the potential to directly impact local communities and the daily lives of rights holders, such as through physical displacement or the loss of economic opportunity.
Forced labor
Modern slavery remains one of the most severe global human rights challenges facing our society. According to the latest index, the ILO estimates that nearly 50 million people are victims of modern slavery worldwide, including nearly 28 million people trapped in forced labor.1 Of the forced labor victims, over 17 million are being exploited through forced labor in the private sector.1 Modern slavery occurs across every region of the world and can materialize in any global supply chain. We aspire to do our part to help prevent and eradicate forced labor.
Freedom of association
Freedom of association refers to the right of all workers to join or form a legally-recognized trade union or any other organization. While freedom of association is a fundamental right enshrined in the Universal Declaration of Human Rights and the ILO Declaration on Fundamental Principles and Rights at Work, there are still a variety of challenges in ensuring that it is consistently respected around the world — from interference with the rights of workers to legal restrictions on the right of association.
Human right to water
Water is fundamental to the global food system and to our business. It nourishes the crops used to make our products, serves as an important ingredient in many of our beverages and is an integral component of our manufacturing operations. But, in some regions, water is scarce. As one of the first companies of our size to acknowledge access to water as a fundamental human right, we have a vision to become net water positive. We work to understand water challenges at a local level and support collaborative solutions that address the specific needs of the watershed and the communities that depend on it.
Workplace health and safety
Supporting the health and safety of workers within our supply chain is one of our top priorities as a company. We drive health and safety values throughout our direct operations through our Global Environment Health & Safety Management System (GEHSMS), a cohesive set of management and technical standards for key environmental, health and safety risks across our business. Workplace health and safety is also a critical component of our Supplier Code of Conduct (SCoC), which establishes the expectation that our suppliers proactively manage health and safety risks and provide a safe environment for workers within our supply chain.
Embedding respect
Governance
We believe that strong governance is the foundation for embedding respect for human rights throughout our business. PepsiCo’s Board of Directors (Board) considers sustainability issues to be an integral part of its business strategy oversight. Throughout the year, the Board and the relevant committees, such as the Sustainability and Public Policy Committee, receive updates and discuss sustainability, human capital management and public policy matters with management.
PepsiCo’s Global Human Rights Office is charged with setting and driving the company’s human rights strategy across the business and supply chain. It is led by the company’s Chief Human Rights Officer, who reports directly to our Executive Vice President, General Counsel and Corporate Secretary. The Human Rights Office works closely with leaders across our various business units to operationalize our approach, conduct ongoing human rights due diligence and drive our human rights strategy.
The Human Rights Operating Council (HROC) is a cross-functional group of senior business leaders that supports and advises the Global Human Rights Office on its efforts to embed and operationalize the company’s human rights strategy. The HROC receives progress and trend updates, reviews our due diligence findings and provides ongoing feedback to help shape key initiatives and determine our future priorities.

Policy framework
Our policies play an integral role in our work to embed respect for human rights throughout our business. They help us set clear expectations for our employees and suppliers, and they also establish a framework that helps us monitor compliance with our standards.
Our Global Human Rights Policy outlines the core standards and expectations we have established for our employees in the area of human rights. This policy is incorporated into our Global Code of Conduct (Code) and applies to all PepsiCo employees, including employees of PepsiCo’s consolidated subsidiaries.
Our SCoC outlines the expectations we have of our suppliers in the areas of business integrity and anti-corruption, human rights and labor practices, health and safety and environmental management. We expect our direct suppliers of goods or services to comply with the standards outlined in the SCoC and apply these principles to their supply chain, where possible.
Training and awareness raising
We believe ongoing training and awareness raising are also critical to embedding respect. To support our work in this area, we have established communication channels and training programs for our employees and strategic, tier-1 suppliers. These programs help us raise awareness of potential issues, communicate our policies and standards, and provide guidance on how to help prevent, identify and respond to potential human rights issues, such as forced labor.
Engaging our employees
Every year, we require employees at all levels of the company to complete a training on our Code. The Code training is designed to educate our employees on their obligation to comply with our Code and the behaviors expected under it, including compliance with our Global Human Rights Policy. More information on our 2024 trainings can be found on Ethics and integrity. The Code is regularly communicated to associates through internal communications, as appropriate. In addition to the annual Code training, in 2024, PepsiCo’s Human Rights Office conducted training sessions with nearly 800 PepsiCo employees on topics such as human rights due diligence and forced labor prevention.
Engaging our strategic, tier-1 suppliers
Our Global Human Rights Due Diligence Program engages our strategic, tier-1 suppliers of our key ingredients and materials and helps build capabilities on the expectations outlined in our SCoC, including the prohibitions on forced and child labor. In late 2024, we revised our SCoC and the accompanying Supplier Code of Conduct Training to help clarify our expectations and provide additional guidance. We also anticipate launching the revised SCoC and SCoC Training to our strategic, tier-1 suppliers in 2025. In 2024, we also continued to support and catalyze broader industry training and capability initiatives, which included:
- Co-sponsoring an AIM-Progress grievance mechanism capacity building program in Brazil to support local suppliers in improving existing industry-level grievance management systems, and
- Continuing to co-sponsor the AIM-Progress Tackling Forced Labor and Child Labor Initiative, which has trained nearly 800 representatives from sanitation providers, labor providers, and co-manufacturers and co-packers across the food and beverage industry in the United States.
Human rights due diligence
Risk identification
We recognize there are a variety of ways that human rights issues could arise directly or indirectly in the course of our business activities. While we strive to address all potential risks across our business and supply chain, in line with the UN Guiding Principles, we apply a saliency lens to help prioritize our efforts. We take a multidimensional approach to identifying potential risks across our business and supply chain that considers a variety of sources such as external risk indices, supplier assessment and audit findings, input from internal and external experts and analysis of industry trends.
Our due diligence process
We have established a due diligence process that helps us assess potential human rights risks in our business and direct supply chain, integrate insights into our internal systems, track the effectiveness of our actions and communicate our progress. Underlying this process is our Global Human Rights Due Diligence Program which helps us assess, identify and remediate impacts in our business and direct supply chain. Learnings and insights from this program are integrated into our internal processes to help develop appropriate policies and systems.
Owned operations
Our Global Human Rights Due Diligence Program utilizes a risk-based approach to assess, mitigate and address potential impacts across our nearly 300 company-owned manufacturing sites worldwide. Audits are semi-announced and conducted by independent, third-party auditors and leverage SMETA 2-Pillar protocol requirements to help promote ongoing compliance with local law, PepsiCo’s policies and international human rights standards.
Strategic, tier-1 suppliers
For our strategic, tier-1 suppliers of key ingredients and materials, as well as contract manufacturing and co-packing locations worldwide, our Global Human Rights Due Diligence Program utilizes scored self-assessments and semi-announced third-party audits to identify and assess potential impacts of human rights, labor practices and environmental issues. Audits are also conducted by independent, third-party auditors and leverage Sedex Members Ethical Trade Audit (SMETA) 4-Pillar protocol requirements to help promote ongoing compliance with local law, PepsiCo’s Global Supplier Code of Conduct and international human rights standards.
Addressing non-compliances
Non-compliances identified through our assessments or audits are addressed through the implementation of corrective action plans by the supplier, which have a set timeframe depending on the type and severity of the non-compliance.
Stakeholder engagement
Our engagement approach focuses on an ongoing dialogue with a wide range of stakeholders, including workers, NGOs, trade unions, investors and customers, to gain both global and local perspectives on areas like the design of our approach, management of our salient human rights issues and the overall performance of our program. We also recognize the importance of capturing the voice of rights holders through this process, and we are committed to engaging with potentially and actually affected rights holders in the development and management of our human rights approach.
Throughout the year, we regularly engage with a wide range of stakeholders through a variety of engagement mechanisms such as direct consultations, worker roundtables, landscape programs and multi-stakeholder collaborations.
Grievance management
We recognize that our policies and programs may not prevent all adverse impacts in our operations and supply chain. Our aim is to provide or cooperate in effective remedy where we have caused or contributed to those impacts and to encourage our suppliers to help enable remedy where we learn there are impacts directly linked to our business operations or products. To help facilitate this process, we have established several avenues that allow our employees, and other stakeholders to raise grievances and seek remedy.
Our owned operations
All PepsiCo employees have an obligation to report suspected violations of our Code, policies, or applicable law. Our employees have multiple channels for reporting issues and seeking advice, including their manager, Human Resources, the Law Department, the Global Compliance and Ethics Department and our Speak Up hotline. Speak Up is a toll-free ethics hotline operated by an independent third-party that provides PepsiCo employees, consumers, suppliers, business collaborators and community members with a 24/7, anonymous and confidential means of reporting suspected violations. Speak Up is accessible anywhere in the world, with dedicated toll-free phone lines in more than 70 countries in multiple languages and by web in 28 languages. Our latest report can be viewed here.
Our direct supply chain
We expect our direct suppliers to operate with the same high standards of integrity to which we hold ourselves. This expectation includes having an effective grievance management system in place for their operations and prohibiting potential retaliation against individuals who raise concerns. To complement their systems, their employees and contractors may also report suspected violations of our policies and standards through the PepsiCo Speak Up Hotline, which is made available through our SCoC and Supplier Training.
Strategic collaboration
We participate in a variety of multi-stakeholder groups and collaborative initiatives aiming to enhance our knowledge of specific issues, to drive industry-wide progress and to help address systemic challenges facing our industry. Several of these groups include AIM-Progress, the Sedex Stakeholder Forum, the Consumer Goods Forum and the Leadership Group for Responsible Recruitment.
What's next?
We hope to continue using our unique size and scale to help advance respect for human rights within our business and supply chain, prioritizing action to address our salient human rights issues. In particular, we plan to take action to:
- Continue to embed human rights throughout our processes and to operationalize our human rights strategy within our operations and supply chain.
- Continue to expand our training and capability initiatives, with a focus on raising awareness and strengthening our employees' and suppliers' ability to identify and respond to modern slavery risks.
- Explore new and innovative ways of evaluating the performance of our human rights program, working with experts and external stakeholders to review and evolve our current metrics and performance indicators.
- Actively engage in multi-stakeholder initiatives through collaborative efforts and with governments to drive industry-wide progress and help address systemic human rights challenges.
1ILO, Walk Free & IOM. (2022). Global Estimates of Modern Slavery
Related topics
Agriculture, Climate change, Environment, health and safety, Ethics and integrity, Palm oil, Water
Downloads
Last updated
August 28, 2025