ESG Topics A-Z
Human rights
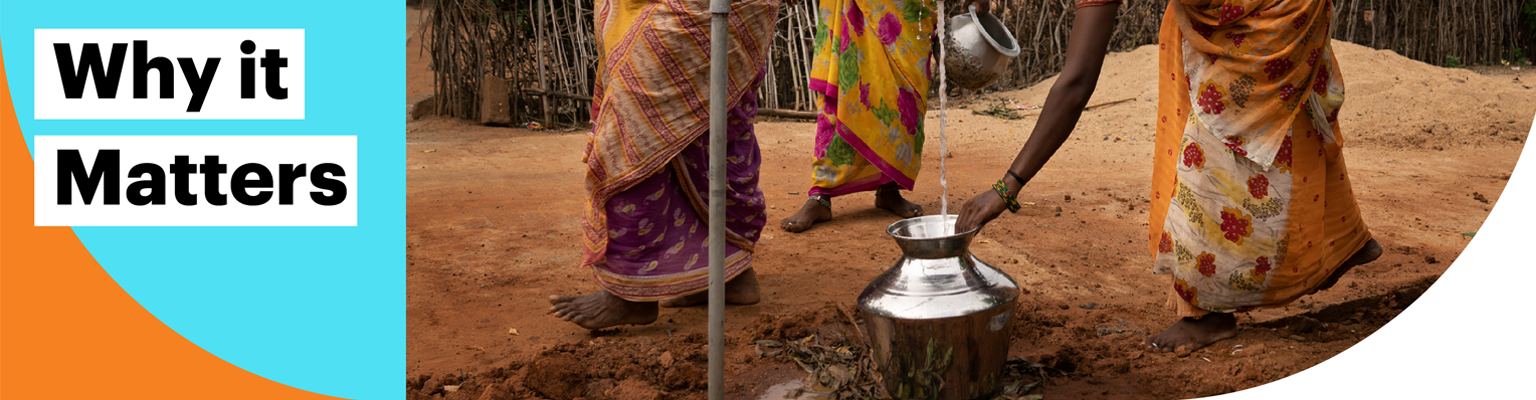
To PepsiCo:
Human rights abuses of any kind are unacceptable. We have a responsibility to help respect human rights within our business and supply chain. PepsiCo can be a positive influence, promoting respect for human rights across our supply chain and aiming to take action to address impacts wherever we uncover them.
To the World:
All people have the inalienable right to life, liberty, work and education, as well as the freedom to express opinions and the freedom from slavery and torture. These and other fundamental human rights are enshrined in the Universal Declaration of Human Rights and the ILO Declaration of Fundamental Principles and Rights at Work. Challenges nevertheless exist in ensuring that human rights are consistently respected around the world — from interference with the rights of workers to legal restrictions on the right of association.
Approach
We are a global company with a complex supply chain that spans multiple tiers, hundreds of countries and territories. A management approach is required as we work to prevent, identify and address potential human rights impacts. Our approach is grounded in the United Nations (UN) Guiding Principles on Business and Human Rights (UNGPs) and is based on the following pillars:
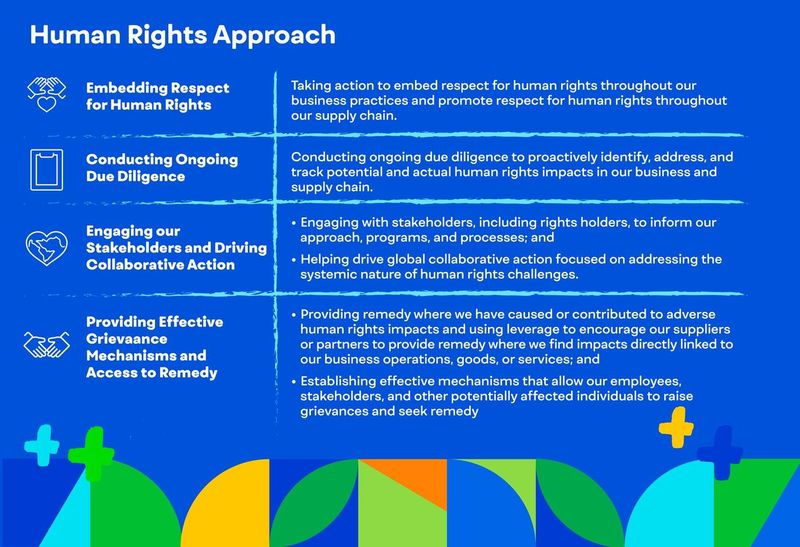
Salient issues
With this approach as our foundation, we prioritize our efforts by focusing on our salient human rights issues — the human rights at risk of the most severe negative impacts through our company activities. This process aims to ensure that we have the appropriate policies and procedures in place to help prevent and address potential human rights risks within our business and supply chain. We also work on a variety of related issues through our broader pep+ (Positive Positive) agenda. We closely monitor emerging issues and regularly review our salient issues to help ensure alignment with emerging best practices and external stakeholder feedback.
Further detail on our salient issues are available below:
- Climate change
- Fair pay and employment conditions
- Land rights
- Forced labor
- Freedom of association
- Human right to water
- Workplace health and safety
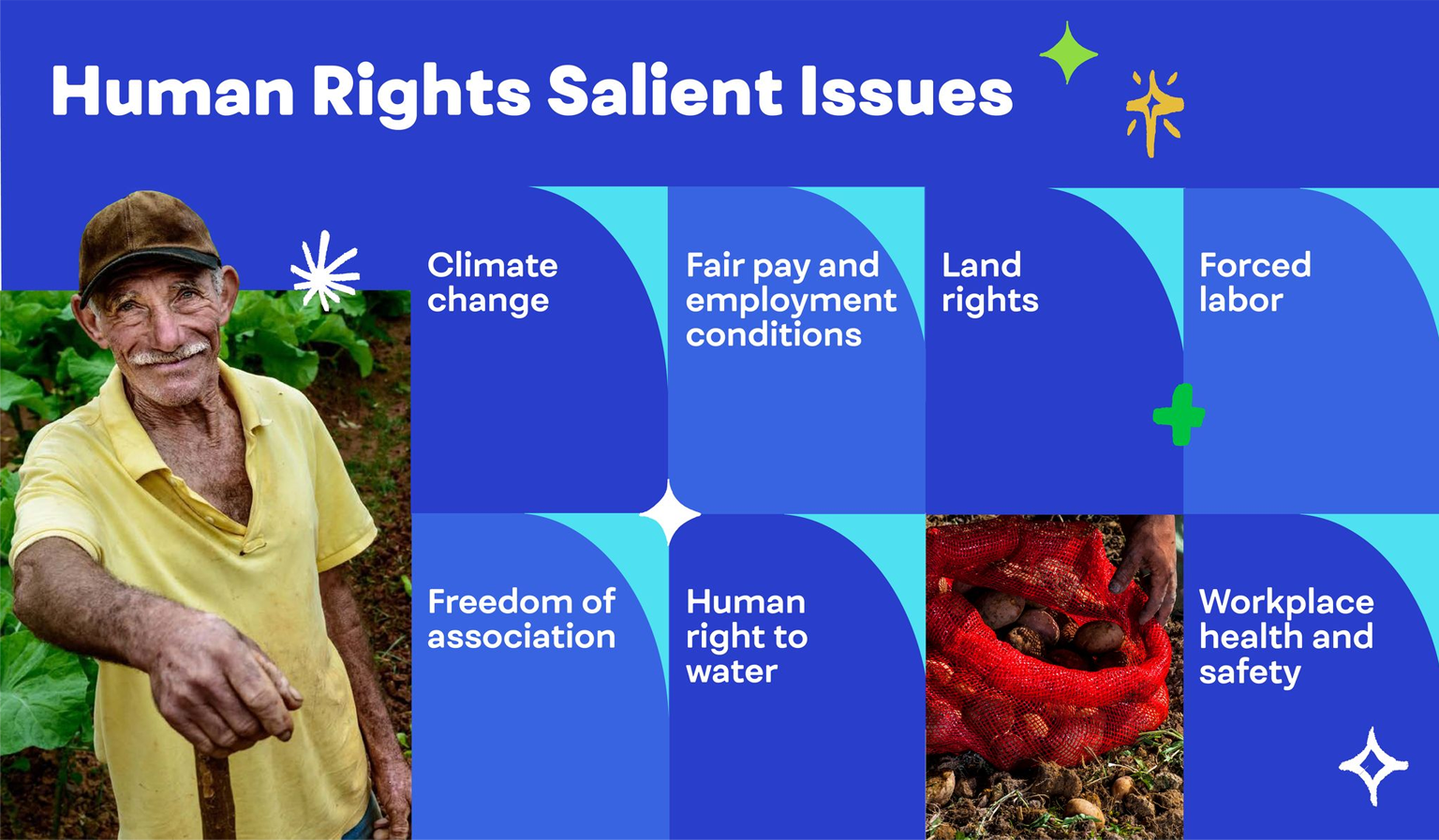
Climate change
Climate change and human rights are inextricably linked, and we recognize that the direct and indirect effects of climate change are often felt by the most vulnerable people and groups among us. We have, and plan to continue to embed a human rights lens into our mitigation and resilience efforts to help respond to potential climate-related human rights impacts. We will also strive to support a just transition for vulnerable groups within our supply chain, maximizing the social and economic opportunities stemming from our Climate Transition Plan, while minimizing and carefully managing the risks. Doing so is a business imperative, and we aim to engage with affected and potentially affected rights holders, including our employees, supply chain workers and the local communities in which we operate.
Fair pay and employment conditions
Given the complexities of the manufacturing and agriculture sectors, workers in these industries are at a higher risk of facing potential adverse human rights impacts related to working conditions and fair pay, such as excessive working hours and lack of adequate rest periods. We believe that everyone should earn a wage sufficient to afford a decent standard of living, and we have established several initiatives aiming to help advance fair pay and employment conditions throughout our direct operations and supply chain. We have established policies to help guide working hours, overtime and rest periods for workers in our operations and supply chain.
Land rights
Secure land rights are a vital component of economic prosperity, sustainable food production and the responsible use of natural resources. This can be particularly true in developing countries and areas inhabited by indigenous communities, yet recent estimates indicate that only 30% of the world’s population has a legally registered title to their land.1 Land rights issues have the potential to directly impact local communities and the daily lives of rights holders, such as through physical displacement or the loss of economic opportunity.
Forced labor
Modern slavery remains one of the most severe global human rights challenges facing our society. The ILO currently estimated that nearly 50 million people are victims of modern slavery worldwide, including nearly 28 million people trapped in forced labor.2 Of the forced labor victims, over 17 million are being exploited through forced labor in the private sector.2 Modern slavery occurs across every region of the world and can materialize in any global supply chain. We aspire to do our part to help prevent and eradicate forced labor.
Freedom of association
Freedom of association refers to the right of all workers to join or form a legally-recognized trade union or any other organization. While freedom of association is a fundamental right enshrined in the Universal Declaration of Human Rights and the ILO Declaration on Fundamental Principles and Rights at Work, there are still a variety of challenges in ensuring that it is consistently respected around the world — from interference with the rights of workers to legal restrictions on the right of association.
We respect the right of freedom of association, and this principle is embodied in our Global Code of Conduct, Global Human Rights Policy and Global Supplier Code of Conduct (SCoC).
Human right to water
Water is fundamental to the global food system and to our business. It nourishes the crops used to make our products, serves as the main ingredient in many of our beverages and is an integral component of our manufacturing operations. But, in some regions, water is scarce. Climate change is also increasing pressure on water resources around the world, with recent estimates indicating that two-thirds of the world’s population will live in water-stressed regions by 2025.3 As one of the first companies of our size to acknowledge access to water as a fundamental human right, we have a vision to become net water positive. We work to understand water challenges at a local level and support collaborative solutions that address the specific needs of the watershed and the communities that depend on it.
Workplace health and safety
Supporting the health, safety and well-being of workers within our supply chain is one of our top priorities as a company. We drive health and safety values throughout our direct operations through our Global Environment Health & Safety Management System (GEHSMS), a cohesive and comprehensive set of management and technical standards for key EHS risks across our business. Workplace health and safety is also a critical component of our SCoC, which establishes the expectation that our suppliers proactively manage health and safety risks and provide a safe environment for workers within our supply chain.
Human rights governance
We believe that strong governance is essential to successfully embedding respect for human rights across our business. Our global governance structure is responsible for overseeing and managing human rights at various levels throughout our business, with our Board of Directors, Senior Leadership and Chief Human Rights Officer serving central oversight and management roles.

Board of Directors (Board)
The Board plays an essential role in determining our strategic priorities and considers ESG issues (including human rights) as an integral part of its business oversight. To this end, the Board established a Sustainability and Public Policy Committee to assist them in providing more focused oversight of key sustainability, inclusion and public policy matters.
Senior leadership
Embedding sustainability within our business requires the commitment of our senior leadership, who drive the necessary mindset throughout their respective areas of oversight. Our Chairman & CEO, his direct reports and top functional leaders have direct oversight of the sustainability agenda (including human rights), strategic decisions and performance management and receive updates regularly. This ensures that sustainability is a key accountability factor for every member of our senior leadership team.
Global Human Rights Office
Our Global Human Rights Office is led by PepsiCo’s Chief Human Rights Officer (CHRO) who also serves as Senior Vice President and Chief Counsel for Global Human Resources at PepsiCo, reporting directly to our Executive Vice President, General Counsel and Corporate Secretary. It is a dedicated team within our Law Department that is responsible for driving our global human rights strategy, managing progress against our goals and our salient human rights issues. The team oversees our human rights due diligence programs and works closely with other internal stakeholders such as Human Resources, Global Sustainability, Sourcing and Procurement on implementing our strategy within our business and supply chain.
Our Human Rights Office is tasked with delivering the human rights program for our own operations and supply chain. Its members have clear annual performance targets that link their compensation with the performance of our human rights program. This includes their responsibility for a wide range of human rights issues, including Forced labor.
Human Rights Operating Council (HROC)
PepsiCo’s HROC is a cross-functional group of senior corporate and sector leaders that support our CHRO and advise the Human Rights Office on actions to address human rights risks in our supply chain. The HROC meets periodically to review our due diligence findings, monitor emerging trends and risks and discuss and integrate stakeholder feedback into our due diligence approach.
Embedding respect
Our policies play an integral role in our work to embed respect for human rights throughout our business. They help us set clear expectations for our employees and suppliers, and they also establish a framework that helps us monitor compliance with our standards. In 2022, we published our updated Global Human Rights Policy.
We also believe that building and strengthening the capacity of our employees and suppliers is an important step in helping identify, mitigate and respond to potential human rights issues within our business and supply chain. We refreshed our capacity building approach and resources in 2022, delivering tailored trainings and guidance materials to our employees and select suppliers on issues such as responsible recruitment.
Human rights due diligence
We have established a due diligence process that assesses potential human rights impacts within our business and supply chain, integrates its findings into our internal systems, tracks the effectiveness of our actions and regularly communicates our progress. Our due diligence process focuses first on our direct operations and strategic, direct tier-1 suppliers.
Our process utilizes a risk-based approach to help monitor risk and assess, identify and remediate potential impacts within our business and supply chain. When needed, we may increase the frequency and/or type of due diligence assessment in response to new events such as entry into new markets, onboarding of new suppliers or emerging human rights challenges in certain markets.
We are continuing to expand our due diligence programs to integrate new assessment tools and to cover additional areas of our supply chain, including our third-party labor providers and transportation and logistics providers. We also regularly integrate new assessment tools into our due diligence process. For example, in 2021, we piloted an independent remote worker voice initiative in the United States, which we expanded to additional worker groups in Mexico, Egypt and Saudi Arabia in 2022. Learnings and insights from our due diligence programs are regularly integrated into our internal processes to help ensure that we have the appropriate policies and management systems in place to prevent, identify and address potential human rights risks within our business and supply chain.
Stakeholder engagement and collaborative action
We believe that an open and continuous dialogue with our stakeholders is critical to helping inform our human rights program. Our engagement approach focuses on an ongoing dialogue with a wide range of stakeholders, including workers, NGOs, trade unions, investors and customers, to gain both global and local perspectives on areas like the design of our approach, management of our salient human rights issues and the overall performance of our program. We also recognize the importance of capturing the voice of rights holders through this process, and we are committed to engaging with potentially and actually affected rights holders in the development and management of our human rights approach.
Throughout the year, we regularly engage with a wide range of stakeholders through a variety of engagement mechanisms such as direct consultations, worker roundtables, landscape programs and multi-stakeholder collaborations.
Grievance mechanisms and access to remedy
We recognize that our policies and programs may not prevent all adverse impacts in our value chain. Our aim is to provide or cooperate in effective remedy where we have caused or contributed to those impacts and to use our leverage to encourage our suppliers to help enable remedy where we learn there are impacts directly linked to our business operations or products. To facilitate this process, we have established a variety of mechanisms that allow our employees, stakeholders and other potentially-affected individuals to raise grievances and seek remedy. Data and insights from these mechanisms are regularly reviewed by our Human Rights Office to identify trends within our business and supply chain and integrate learnings into our approach and due diligence programs.
Our direct operations
All PepsiCo employees have an obligation to report suspected violations of our values, Global Code of Conduct, policies or applicable law. Our employees have several avenues for reporting issues and seeking advice, including their manager, Human Resources, the Law Department, the Global Compliance and Ethics Department and our Speak Up hotline.
Speak Up is a toll-free ethics hotline operated by an independent third-party that provides PepsiCo employees, consumers, suppliers and business partners and community members with a 24/7, anonymous and confidential means of reporting suspected violations. These reports are used to drive organizational changes and a better work environment, including through training, policy revision and process enhancements. Speak Up is accessible anywhere in the world by dedicated toll-free phone lines in more than 60 countries in multiple languages and by web in 26 languages. We regularly publish information on the usage of our Speak Up hotline, including the total number of reports and their categorical distribution. Our latest report can be viewed here.
Our supply chain
We expect our suppliers to operate with the same high standards of integrity to which we hold ourselves. This expectation includes having an effective grievance management system in place for their operations and prohibiting potential retaliation against individuals who raise concerns. To complement their systems, their employees and contractors may also report suspected violations of our policies and standards through the PepsiCo Speak Up Hotline, which is made available through our SCoC and Supplier Training.
We have also established a grievance mechanism for our agricultural supply chain to complement our existing Speak Up program and to help us manage environmental and social concerns raised about our supply chain. The mechanism allows third parties to raise concerns that our environmental and social policies are not being upheld in our agricultural supply chain. Our approach is set out here.
In 2023, we continued to evolve our agricultural grievance mechanism by enhancing its data collection and traceability processes to support its ongoing management of stakeholder concerns. Our management process includes an initial investigation into every grievance submitted to determine whether it is “in scope” or “out of scope” of the agricultural grievance mechanism.4 If a grievance is deemed “in scope,” it progresses to the engagement phase where PepsiCo works with the appropriate supplier to assess the situation.
Progress
In 2023, our Human Rights Office continued to partner with our global functions and sector businesses to embed and operationalize our global human rights approach. This included deploying our market-level due diligence guidelines in key markets to conduct enhanced risk assessments, targeted due diligence and tailored trainings to build capability and help identify potential risks specific to our local business models and sourcing practices. We did the following:
- Conducted a review of our global human rights due diligence process, implementing actions to reinforce our risk-based approach, strengthen our management systems and enhance our assessment methodology.
- Expanded our global human rights training program, deploying targeted trainings to key functional and sector teams to strengthen our ability to mitigate and address potential human rights risks within our business and supply chain.
- Continued to catalyze collaborative action aiming to help address forced labor risks through industry initiatives such as the Consumer Goods Forum and AIM-Progress, focusing on high-risk markets.

Progress
- Launched a dedicated combating modern slavery training to nearly 2,000 PepsiCo employees across key global functions (e.g., Law Department, Compliance and Ethics, Corporate Affairs, Procurement and Sourcing).
- Provided open-access online training to help our direct, business-critical suppliers better understand the principles of our SCoC.
- Deployed targeted trainings to select suppliers on priority topics such as forced labor and responsible recruitment.
- Assessed 62 of our company-owned manufacturing operations across 27 countries. Furthermore, we conducted or recognized 885 on-site or virtual audits5 of our business-critical tier-16 suppliers across 70 countries and territories.
Challenges
The complexity of our supply chain, which spans multiple tiers and hundreds of countries, requires ongoing partnership and collaborative actions to help address the systemic challenges facing our business and the communities in which we operate.
Strategic partnerships
We participate in a variety of multi-stakeholder groups and collaborative initiatives aiming to enhance our knowledge of specific issues, to drive industry-wide progress and to help address systemic challenges facing our industry. Several of these groups include AIM-Progress, the Sedex Stakeholder Forum, the Consumer Goods Forum and the Leadership Group for Responsible Recruitment.
What's next?
We hope to continue using our unique size and scale to help advance respect for human rights within our business and supply chain, prioritizing action to address our salient human rights issues. In particular, we plan to take action to:
- Continue to embed human rights throughout our pep+ pillars and processes and to operationalize our human rights strategy within our operations and supply chain.
- Continue to expand our training and capability initiatives, with a focus on raising awareness and strengthening our employees' and suppliers' ability to identify and respond to modern slavery risks.
- Work toward publishing a revised SCoC to help ensure alignment with stakeholder feedback, emerging regulatory developments and internationally recognized best practices.
- Explore new and innovative ways of evaluating the performance of our human rights program, working with experts and external stakeholders to review and evolve our current metrics and performance indicators.
- Actively engage in multi-stakeholder initiatives through collaborative efforts and with governments to drive industry-wide progress and help address systemic human rights challenges.
1The World Bank. (2017) Why Secure Land Rights Matter
2ILO, Walk Free and IOM. (2022) Global Estimates of Modern Slavery
3United Nations. (2016) Secretary-General Warns Two Thirds of Global Population Could Face Water-Stressed Conditions within Next Decade, in Message for International Forests Day
4Our Agricultural Grievance Mechanism covers issues raised that allegedly involve a direct supplier or indirect supplier to PepsiCo
5Virtual audits are offered in limited circumstances
6Tier-1 suppliers are the direct suppliers of PepsiCo
Downloads
Last updated
June 20, 2025